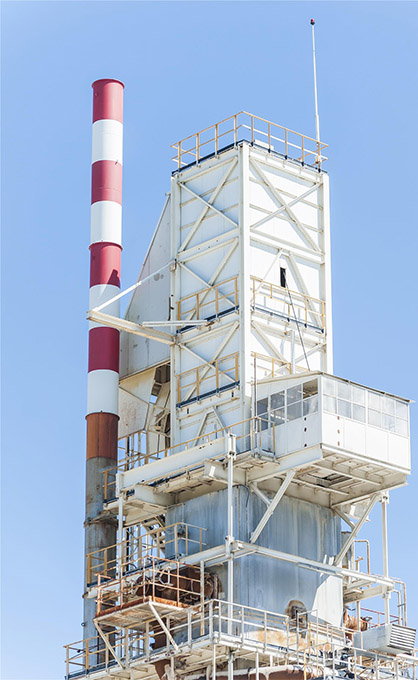
With the rapid development of PSA technology, the application of PSA technology in the chemical industry has become increasingly common. PIONEER has built more than 80 PSA oxygen plants, CO plants and hydrogen plants for customers in the chemical industry and is the professional PSA technology provider for petrochemical and coal chemical enterprises.
A. Get oxygen-enriched air to participate in the reaction.
B. PSA oxygen production technology can be used to produce oxygen-enriched gas that is needed in synthetic ammonia production.
C. PSA oxygen production technology can be used to produce oxygen for the desulfurization process.
Case
PKU PIONEER has built a VPSA oxygen equipment for Hindustan Petroleum Corporation Ltd.(HPCL) for sulphur recovery unit block, the capacity is 6422 Nm3/h, oxygen purity is 93%. Hindustan Petroleum Corporation Ltd., incorporated in the year 1952, is a large cap company (having a market cap of Rs 44533.72 Crore) operating in petroleum sector.
A. Use coal, natural gas and heavy oil as raw materials to produce synthesis gas, and use PSA technology to purify CO.
B. PSA technology can be used to obtain high-purity CO products from CO-containing tail gas generated during chemical production, such as calcium carbide furnace tail gas and acetic acid tail gas.
Case
After the 1st phase of the calcium carbide furnace exhaust to 50,000 tons/year ethylene glycol project was successfully put into operation, Xinjiang Tianye Group continued to adopt PIONEER’s proprietary technology. The two parties signed the Phase II contract of calcium carbide furnace exhaust comprehensive utilization to 200,000 tons/year ethylene glycol and to 170,000 tons/year 1,4-butanediol project for PSA-CO and H2 purification system. The units designed and built by PIONEER for this project are the PSA-CO plant (24000Nm3/h, ≧ 99.5%), and the PSA-H2 plant (31000Nm3/h, ≧ 99.9%) for calcium carbide furnace tail gas separation , meanwhile, PIONEER will also undertake the construction of the PSA-H2 plant (55,000 Nm3/h, ≧ 99.9%) for methanol purge gas separation. The CO and H2 products are both used for downstream production of ethylene glycol and 1,4-butanediol. After the project is put into production, Xinjiang Tianye Group will reach an annual production capacity of 250,000 tons of ethylene glycol and 200,000 tons of 1,4-butanediol.
A. Hydrogen-containing tail gases generated in industrial production, such as exhaust gas from methanol synthesis, methanol-fueled exhaust, demethanizer tail gas and tail gases from various pyrolysis processes all contain a certain amount of hydrogen. Hydrogen can be obtained for customers from these industrial tail gases through PSA separation.
B. Use coal, natural gas and heavy oil as raw materials to react with steam to make gas, and use PSA technology to purify hydrogen.
Case
The 240,000 tons per year ethylene glycol project of Jianyuan Coal Coking CO., LTD. As raw material, 64500 nm3 /h coke oven gas has process of storage, pressurized, pure oxygen no-catalytic conversion, decarburization-desulfurization, desulfurization, syngas purification, ethylene glycol synthesis and rectification for 240000 tons ethylene glycol production per year.
Beijing Peking University Pioneer Technology Co., Ltd. Supplies CO separation plant (25098Nm3/h, purity>99%) and H2 plant (53512Nm3/h, purity>99%) for coke oven gas in this project.