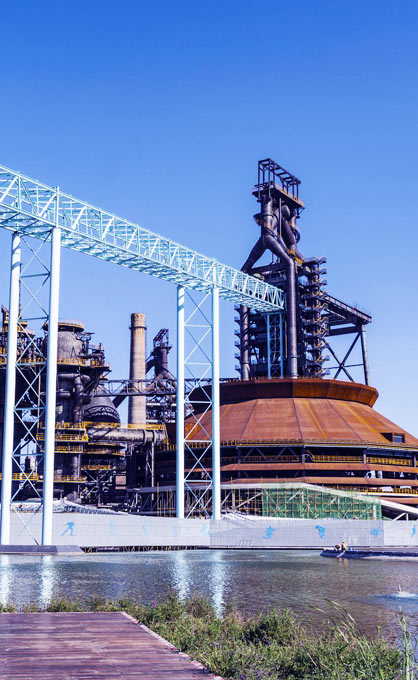
1. Oxygen-enriched combustion in ironmaking blast furnaces
Oxygen-enriched combustion in ironmaking blast furnaces: PSA oxygen production technology can provide stable and high quality oxygen products for blast furnace ironmaking. In the 21st century, with the development and progress of low-energy BF special oxygen generation technologies, such as PSA oxygen generation technology and oxygen enrichment before the blower, China’s BF oxygen enrichment and PCI technology has once again made a leap-forward progress and ranked at the world’s leading level.
There are two methods of BF oxygen enrichment: oxygen enriched before and after the blower.
The common oxygen enrichment after the blower is an oxygen enrichment method that depressurizes the high-pressure high-purity oxygen at the air separation outlet, sends it to the back pipe of the blast furnace blower, mixes it with the air, and then blows it to the blast furnace, causing great energy waste. The oxygen enrichment before the blower refers to an oxygen-enriched blast method in which low-pressure oxygen is directly mixed into the suction side of the blast furnace blower, so as to increase the oxygen content in the blast. With reference to relevant information, the power consumption of BF oxygen enrichment before the blower is only 60% of that of BF oxygen enrichment after the blower.
If the concentration of oxygen entering the BF blower is controlled within a reasonable range, the BF blower does not need to be reformed, and oxygen enrichment before the blower can be realized only by adding or regulating pipelines, valves and airflow distributors. At present, many iron and steel plants have adopted or transformed into the method of oxygen enrichment before the blower, which has brought considerable economic benefits.
Case
The ZO-15000/80 VPSA oxygen generation project, which was built by PKU PIONEER for a Hebei iron and steel company in 2016, was successfully put into operation at one time. The project adopts the method of oxygen enrichment before the blower with an oxygen enrichment rate of 3-5%, the molten iron production is increased by 10-20%, coal ratio is increased by about 35 kg/t·iron, and oxygen comprehensive production cost is lower than 0.3 yuan /Nm3. Based on the price difference between coke and coal as well as the rate of production growth, the annual economic benefits can exceed 30 million yuan.
2.Oxygen-enriched combustion for EAF steelmaking: oxygen can be obtained using PSA technology.
Flow Chart:
After years of development, the EAF steelmaking technology has made great progress. The application of a large amount of oxygen in the EFA steelmaking can not only help accelerate decarburization, whilst the heat released in the oxidation reaction is fully utilized to achieve energy saving and consumption reduction. The technologies of aerobic burner, oxygen-blowing accelerated melting and decarburization in molten pool, oxygen lance and secondary combustion technologies are all enhanced oxygen utilization technologies, combination of which can improve the effect of mixing in the molten pool, promote the metallurgical reaction, reduce the power consumption and increase the productivity.
At present, there are more than 100 electric arc furnaces in the world equipped with VPSA oxygen generators, which are widely applied in foreign countries. The long-term practice shows that VPSA oxygen generators can meet the requirements of EAF steelmaking.
Case
Luzhou Yixin has four electric arc furnaces, among which the largest capacity is 700,000 tons. Since the oxygen supply to the steelmaking was previously satisfied by purchasing liquid oxygen, the production cost has increased with the rise of liquid oxygen price. Therefore, PIONEER designed the VPSA oxygen generators with a capacity of 5,700Nm3/h and the oxygen purity of 93%. Such VPSA oxygen generators have showed satisfactory operation since their first production commencement in November 2018. The production and purity of the oxygen have reached the objective indicators, and the steel products are transported downstream for steel bar production.
3. Steel Tail Gas Purification
A. Recycling blast furnace gas: PIONEER’s PSA CO separation technology can produce CO from blast furnace gas at 99.99% purity.
B. Recycling converter gas: PIONEER’s PSA CO separation technology can produce CO from converter gas at 99.99% purity.
C. Recycling coke oven gas: PSA hydrogen production technology can purify hydrogen in coke oven gas.
Case
Hengyang Valin Steel Pipe Co., Ltd. (hereinafter referred to as “Hengyang Steel”) is a specialized seamless steel pipe manufacturer with production capacity of annual production of 1 million tons of iron, 1.2 million tons of steel, and 1.5 million tons of pipes. BFG annual output is about 21×108 m3, mainly for hot blast stove (about 35%), sintering furnace (about 2%), mixed with natural gas for rolling furnace (about 38%), and most of the remainder is emitted; highest BFG emission rate is up to 29%, and the lowest can only be reduced to about 23%. In order to meet the needs of fuels with high calorific value, Hengyang Steel needs to purchase gas, and blend with blast furnace gas, to improve calorific value of blast furnace gas, for use of steel rolling heating furnace. This has resulted in a serious contradiction between Hengyang Steel’s large demand for gas with high calorific value and failure in effective utilization of gas with low calorific value. To purify BFG to get gas of high calorific value has become wise choice for Hengyang Steel’s energy efficiency.
In 2012, Beijing Peking University Pioneer Technology Co., Ltd. (“PKU PIONEER”) and Valin Hengyang Steel reached cooperation agreement on design and construction of blast furnace gas CO purification plant, currently the plant has been successfully put into operation, with stable operation, excellent indicators, average consumption of raw gas reaching 60,000 Nm3/h, average product gas volume of 18,000 Nm3/h, and CO yield of about 93%. The concentration of CO in the product gas can be adjusted in the range of 60% to 70% as needed, the product gas can fully meet Hengyang Steel’s downstream users’ needs for calorific value, and effect of energy saving and income increase is remarkable.